纤维增强复合材料冲击失效试验
纤维增强复合材料因其优异的比强度、比刚度和可设计性,在航空航天、汽车制造、风电叶片等领域获得广泛应用。然而,冲击载荷下的失效行为是其工程应用中的关键瓶颈问题。本文系统介绍冲击失效试验的检测范围、项目、方法及仪器,为材料性能评估提供技术参考。
一、引言
纤维增强复合材料在受到低速或高速冲击时,往往会产生基体开裂、纤维断裂、层间分层等复杂损伤模式,这些内部损伤难以通过目视检测发现,却会显著降低结构承载能力。据统计,航空复合材料结构中60%的意外失效与冲击损伤相关。因此,通过标准化试验量化材料的冲击失效特性,对产品安全设计和寿命预测具有重要工程价值。
当前国际通用的测试标准包括ASTM D7136(低速冲击)、ISO 14896(高速冲击)等,试验需科学控制能量水平、边界条件等参数,并综合运用多种检测手段分析损伤机理。
二、检测范围与关键指标
冲击失效试验主要覆盖以下材料体系和应用场景:
- 材料类型:碳纤维/环氧树脂、玻璃纤维/聚酯、芳纶纤维/热塑性树脂等
- 结构形式:单向层合板、编织复合材料、夹芯结构
- 冲击速度范围:
- 低速冲击(2-10 m/s):模拟工具坠落、维护碰撞
- 中速冲击(10-50 m/s):模拟飞鸟撞击、弹射物
- 高速冲击(>50 m/s):弹道防护评估
试验需重点监测的三类性能指标:
- 损伤阻抗:产生特定损伤面积所需的冲击能量
- 损伤容限:冲击后剩余压缩强度(CAI)保持率
- 失效模式:分层面积、凹坑深度、纤维断裂分布
三、检测方法与实施流程
1. 落锤冲击试验(ASTM D7136)
最常用的低速冲击测试方法,试验系统包含:
- 冲击装置:电磁/液压驱动落锤,质量5-30kg可调
- 夹具系统:方形支撑框,中央开口直径125±2mm
- 数据采集:力传感器(量程≥50kN)、激光测速仪(精度0.1m/s)
测试流程包括:
- 试样预处理(23±2℃,50±5%RH环境平衡48h)
- 预设冲击能量(通常25-100J,按厚度调整)
- 实时记录力-位移曲线,计算能量吸收率
- 冲击后30分钟内进行超声C扫描检测
2. 高速气炮冲击试验
用于模拟弹道冲击等极端工况,关键技术参数:
- 发射速度:100-800m/s(通过调整气压控制)
- 弹体类型:钢制半球形弹头(直径12.7mm)
- 高速摄影:Phantom相机(帧率≥100,000fps)捕捉变形过程
3. 损伤表征技术
- 超声检测:采用15MHz探头,分辨率0.5mm,绘制分层分布图
- 工业CT:微焦点CT系统(电压160kV),三维重建内部裂纹
- 电子显微镜:SEM观察纤维/基体界面脱粘形貌
四、检测仪器技术要求
完整试验系统需满足以下关键指标:
- 冲击能量控制误差:≤±5%(需定期校准测力系统)
- 时间同步精度:力传感器与位移采集同步偏差<1μs
- 环境控制:高温试验箱可达180℃,湿度控制±3%RH
- 数据采样率:动态信号采集卡≥1MHz(满足ISO 6603要求)
典型设备配置方案:
- Instron CEAST 9350落锤系统(带温度控制模块)
- Olympus Omniscan MX2超声相控阵仪器
- Zeiss Xradia 520 Versa显微CT系统
五、结论与展望
通过标准化冲击失效试验可获取纤维增强复合材料的能量吸收特性、损伤演化规律等关键数据,为材料选型和结构优化提供依据。试验数据表明:
- 碳纤维/环氧树脂的冲击能量吸收比传统铝合金高3-5倍
- 三维编织结构的分层面积比层合板减少40-60%
- 纳米改性树脂基体可使CAI值提升25%以上
未来发展趋势包括:开发多轴冲击试验系统、建立数字孪生仿真模型、应用AI算法进行损伤预测等。建议在试验设计中重点关注应变率效应和温度-湿度耦合影响,以更真实模拟工程服役环境。
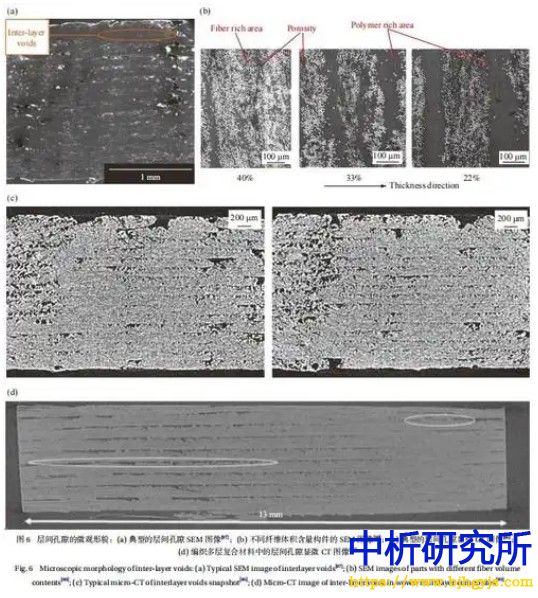
了解中析
实验室仪器
合作客户
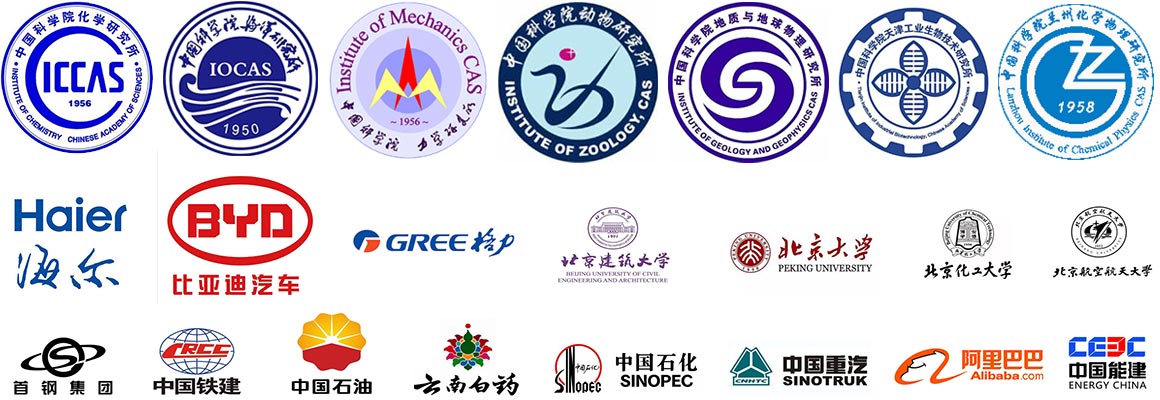